|
|
纵论DCS 展望EPA |
――中控科技集团有限公司董事长褚健先生专访 |
2004-10-15 16:34:00 浙江中控技术有限公司 供稿 |
谈及中国自动化发展的历史,不能不提的是DCS。在顺序控制、传动控制、运动控制等领域,中国的控制技术均处于落后的位置,未能形成强势的产业规模。但唯独DCS,能在技术上与国外保持同步甚至超前,并已形成产业规模,具备相对的竞争优势。这些,应得益于以浙大中控、和利时、上海新华等为代表的国内DCS厂商多年来的不懈努力。 2004年中国自动化学会理事会期间,中国工控网就中国DCS发展及EPA标准专访了浙大中控(现中控科技集团有限公司)董事长褚健先生。 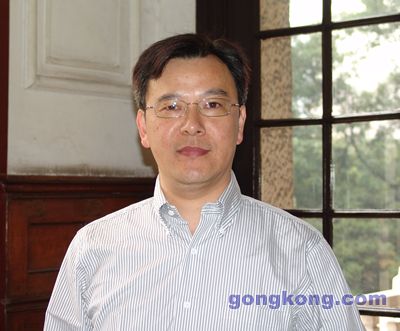 中国工控网: 自20世纪70年代中期Honeywell推出第一台DCS至今,DCS已有30年的历史了。在中国,DCS研究起于何时,其发展的标志又是什么呢? 褚健: 追溯DCS的发展,就我本人的经历和浙江大学而言,应始于对计算机应用于过程控制的研究。这差不多可以追溯到60年代初期。那时,我们学校(浙江大学)就开始从事计算机应用于过程控制的研究,并于1964年在上海炼油厂开始从事实际应用的开发与研究工作。国内第一台真正意义上的工控机是我们与上海热工所共同研制开发的JS-90机。在我的记忆中应该是在七十年代末期开发完成的。JS-90机是可以投入实际应用的真正的工控机,可惜后来学校研究所搬迁的时候,觉得这台机器没有什么价值就废弃了,现在回想起来感觉还是一件非常可惜的事情。 计算机发展到八十年代初期以后,慢慢演变为PC机、工控机,这时,计算机即具备了扩展能力,可以通过输入输出板卡实现控制功能。但这种应用到八十年代中后期开始面临一个问题――冗余,如果不能解决冗余问题,工控机就只是能够单机运行的控制产品,而不能称其为DCS。就我个人而言的DCS探索之路应始于八十年代初期作硕士论文的时候,当时就已经在自己组装输入输出模板,然后与计算机通讯,从而达到控制实验装置的目的,为此还搭了一个三层楼高的精馏塔的实验装置。 中国工控网: 这样看来,应该说我们的DCS的探索之路开始得是很早的。 褚健: 但就浙大而言,第一台DCS的诞生还是在1991年――我们实验室开发的第一套具有冗余功能的工控机,在锦州炼油厂和杭州炼油厂投入使用。虽然该产品当时还处于学校实验室样机阶段,但却是第一个解决冗余技术的。现在,我们浙大中控的“春辉自动化技术长廊”还记载着这段历史。 以1991年我们研发的第一套具有冗余功能的工控机为发端,这时的产品已突破PC的范畴,与现代意义上的DCS比较接近了。在此基础上我们开始进一步研发真正意义上的DCS,并于1993年成立浙大中控公司,真正走上了DCS产业化之路。 就国家宏观发展规划而言,DCS的研发最早是由重庆工业自动化仪表研究所和上海工业自动化仪表研究所牵头进行的,特别是以重庆工业自动化仪表研究所为主,并在当时的国家机械部支持下进行。重庆工业自动化仪表研究所研发的产品是直接以DCS命名的,如第一代国产DCS DJK7500。这是国家的“七五”攻关计划的成果。 中国工控网: 在DCS产业化之路上,浙大中控、和利时以及新华无疑起到了极大的推进作用,您如何看待中国DCS的产业化进程? 褚健: 在DCS发展初期,有相当一批企业在从事DCS的产业化工作,不只是这三家。事实上,DCS产业化之路上还有其它很多企业的足迹。有些企业起初势头很好,但在市场的选择中逐渐没落抑或退出了,其中原因是多方面的。从技术的角度上看,是不是真正的DCS,能不能达到一定的技术指标,能否满足实际应用需求,是决定企业是否生存、发展的一个方面;从市场的角度看,有的公司发展是不错的,但是服务跟不上,是被淘汰的另一个方面,当然还可能存在其它诸多原因。 就你提及的这三家企业,是目前情况最好的几家企业。在产业发展的过程中,这些企业生存下来了,这本身就是一个产业化的过程。应该指出的一点是,这些公司是经过了市场的考验生存下来的,并且均表现出良好的发展势头;这些公司在国内工业自动化产业的发展成就,给不少国内企业以信心,对整个行业有着正面的促进作用。但不只能说我们是科技产业化的榜样,因为很多国内企业在高技术软件产品、硬件产品方面也在不断地向前发展。但在自动化领域,国内DCS企业的发展也至少说明中国还是可以有所作为的。 中国工控网: 国内DCS的产业化道路已经有10年多的时间了,您如何看待DCS的市场前景;国内外DCS厂商各自市场表现如何? 褚健: 可以肯定的是:DCS市场在不断地扩大。从增长情况上看,市场大概保持在50%到60%的年增长幅度。究其原因,首先是中国的经济在不断地发展。流程工业及加工制造业的发展为DCS的应用发展创造了广阔的市场空间,提供了更多的市场机会;其次是传统产业对自动化技术的价值认知度提高了。有许多企业在过去认识不到DCS这一技术的重要性,但是随着技术应用的互相交流,一家企业的使用使其他企业看到了价值,比如说维护成本降低了,总成本降低了,人力资源的占用减少了。可以说“样板式”的案例亦带动了DCS应用的推广。目前,中国有上万家的流程工业企业,所以说市场是非常巨大的。 浙大中控在1993年成立之初的销售额仅有40万元,2001年的时候已经达到了2.6亿元,2004年更可达到7亿元的历史新高,就我们企业自身的业绩来看整个市场,无疑增长是很快的。 从市场表现上看,我个人认为国内DCS厂商的市场表现要比国外厂商更优秀些。就装机量而言,目前国内DCS厂商超过了50%的市场份额;就可靠性而言,我认为国内DCS产品是超过国外产品的,目前只在一些特大型的项目上,国外产品还占据一些优势。当然,在以金额计算的市场份额上,国外厂商应略强于国内厂商。 中国工控网: 从现在市场表现上来看,DCS已被市场广泛认可。DCS历经近30年的发展,虽在原理上没有什么突破,但普遍认为DCS已经历经了三代的发展,目前已有了第四代DCS的概念。您如何看待第四代DCS这一提法。 褚健: 就目前的技术发展而言,已经是无所谓第几代了。第四代DCS概念的提出,可能是一些企业的市场行为、宣传行为。今天的DCS的确在技术上已发生一些变化,但从原理上来讲,与以前的DCS没有本质区别。即便是DCS的发展已进入了第四代,也不能说第三代DCS就将退出市场,只能说现在的发展使DCS更加适应了市场的需求 现在的DCS还是过去大家理解上的DCS,没有发生翻天覆地的变化。但工业以太网技术、OPC技术的引入,确实给新型的DCS赋予了一些新特征。 现在有一种概念叫做混合控制,新型的DCS强调的是信息与集成,集成即是集成过程控制与顺序控制。就混合控制系统而言,过去的DCS也有PLC的功能,但是PLC在DCS里面是比较弱的,因为开关量在DCS系统中并不占有很大的比重。DCS长久以来注重的是模拟量的处理。但随着现代计算机技术的发展,特别是微电子技术的发展,DCS慢慢融合了PLC的顺序控制功能,成为集过程控制、顺序控制及批量控制为一体的混合控制系统。同时,PLC和DCS也在慢慢融合,PLC也在逐渐加强模拟量的处理能力,所以像传统的PLC厂商西门子也推出了自己的DCS。这种技术上的融合是一种自然的趋势,并不是通过这个技术会变成第几代,不是这个概念。 DCS的另一变化是开放。从DCS的关键技术――通信技术上看,比如现在应用的以太网技术,已经非常成熟,这跟过去不同厂家的DCS系统各自使用自有的通信网络是不同的。过去的网络是封闭的,现在的网络是开放的。同时,由于网络结构的开放,带来的是系统结构的开放,比如所有软件必须符合OPC标准,这些都可以理解为第四代。如果DCS继续走封闭之路,是一定会被新的技术淘汰的。 从用户的角度来说,DCS的应用并没有太大的区别――在开放的软件平台上,有自己的个性化平台,有自己的解决方案。把DCS切实地应用于生产,帮助企业提高生产效率,提高产品质量,进而提高企业的效益。 今天,先进控制、实时优化、数据挖掘、数据校正、智能健康维护等等一系列技术也正在基于这个开放的平台得以发挥作用。以DCS为平台的MES(生产过程制造执行系统)应用也已经成为DCS未来的发展趋势。 DCS正在为用户创造更大的附加价值,为提升企业的效益发挥着重要作用。 中国工控网: 有一种说法是FCS将取代DCS,您是怎么看待这个问题的;DCS会不会被一个新的控制系统所取代。 褚健: 一定会的,但是时间会比较长,在短期内是不可能的。 但也不是说DCS被新技术所取代了,就消亡了。主要是随着网络技术的不断发展,整个工业自动化系统也会被网络化,当网络化以后,DCS所涵盖的概念就跟以往不同了。很多控制功能会被拆分,一部分下放到现场仪表,一部分上移到控制室。到那时,不会再有一个大的控制柜,用做输入输出设备――将现场信号送到控制室,然后通过I/O转换为数字量,再通过计算、处理,再输出控制信号。智能仪表将可以直接输出数字量,与控制器通信,完成控制功能。也就是把模拟转换功能移植到现场层。这样,DCS的概念就发生了变化。但并不是说有什么替代了DCS,主要是网络技术的发展,使得现场的变送器都可以达到数字化。 从技术的发展来看,一定是要网络化的。浙大中控联合国内几家研究院所现在共同研究的EPA(Ethernet for Plant Automation)就是把以太网应用到现场设备上。我们制定了EPA的标准,并已将EPA标准提交给国际标准组织审定了。如果现场每一个仪表的芯片都嵌入EPA协议,那么I/O就没有了,DCS的柜子就会变得很小。 DCS在进一步网络化的进程中就会变成服务器。 中国工控网: 谈到EPA,已经成为IEC作为PAS发布的国际标准之一,成为我国第一个拥有自主知识产权的现场总线国际标准,这是非常了不起的一件事。它的发展是怎样的? 褚健: 国际上现在有十几种现场总线标准,标准是不统一的,没有一家厂商愿意放弃自己的标准而改用别的标准。过去的几年中,我们花了很多的精力,投入很长时间在FF方面,包括国内很多单位也在做FF。投入于FF标准其实就是学,可花了这么多年,还是有很多技术没有掌握――不是不能掌握,而是技术壁垒让你无法掌握,真正应用时依旧需要购买芯片、专利。中国现在在用的FF项目有十余个,规模或大或小,中国已然成了FF技术的一个试验场,而国外并没有在大张旗鼓地应用FF。国外用户觉得4~20mA已经很好,对于流程控制来说4~20mA就能够达到控制要求了。目前我们的变送器、温度传感器、流量计的精度就在1%或者0.5%或者更高的0.2%左右,这已经是很高的精度了。在这一源头精度标准下,无论采用32位CPU还是64位CPU,其数字信号的精度都不会提高,因为任何模数转换的精度都不可能超越仪表本身的精度,所以说4~20mA并没有什么不好,因此并不一定要刻意地使用FF。可是FF顺应了数字化网络应用的大趋势,得以成为其进入市场的优势。在如此的数字化网络应用趋势下,到底哪一个标准是适合的呢?这在94、95年我们公司开发第二代DCS的时候,成为我们在网络标准采用上的困惑。当时的以太网只有2M的带宽,那时我们就赌在了以太网上,现在看来我们是成功了,赌对了。这次选择,使我们在以太网领域有了很好的积累,与此同时我们也受到了一些专家、领导的启示,他们就认为从技术上来说以太网应用于工业控制领域是完全可能的,我也做了一些研究,研究的结果是可行的。现在EPA有希望成为一个国际标准,当然以后还有很多工作要做,如各种各样的模块标准化工作等等。 中国工控网: PAS的有效期是3年,这3年我们还要做什么样的工作呢? 褚健: 首先要有大量的应用,且对我们而言作十几个工程应用案例都是很简单的。但只做应用并不能够真正解决它作为一个标准的推广应用。任何一个标准,它不仅仅是一个协议,它还有着很多符合该协议标准的产品开发问题,如PID模块、现场仪表产品等。目前我们做了一个相对复杂的针对于模块应用的协议产品,一旦推出来,技术上就会比较成熟了,届时我们会做出相应的芯片,仪表厂家即可将协议嵌入自己的产品,使之符合EPA协议规范。 同时,一个标准还要有支持这一标准的会员企业。在这方面现有几个国际的大型厂商比如像施耐德就希望跟我们合作。我们希望在作成一个标准以后,要尽可能地开放。从我们涉足标准领域来讲,我们现在还比较弱,影响比较有限,我们将更加彻底地将EPA标准予以开放,以推进其应用。 中国工控网: 开放意味着什么呢,协议也会免费吗? 褚健: 我认为,现在越开放,对我们越是有利,对用户也越有利,对行业也越有利。现在我还说不清具体的开放程度,什么是免费的,但总的一个原则是能开放的全部开放,尽可能地使更多的人,以最低的代价或者是没有代价来使用这个协议。 使用一个标准协议不付出一些是不可能的,但是我们要让使用EPA标准协议的费用在整个产品的成本中占的比重小到可以忽略不计,这样,价格优势就完全可以体现到用户那里,这样做的直接影响是价格的整体下降,带动的是制造成本的下降。这样对于生产来说,可以保证用户采用EPA这种新技术是绝对优化的方案。 中国工控网: EPA是中国工业自动化领域第一个被IEC接受的标准,其意义非凡啊! 褚健: 意义我觉得有几方面,首先,就像我们在做DCS,让大家觉得中国人还是可以有所作为的;其次,如果EPA是成功的,那么整个自动化产业,特别是过程控制,都会产生很大的变革,也许我们就不用昂贵的FF了,因为变送器可以全部采用EPA的协议,我们能不能做到,只要插上网卡就可以了呢?如果能做到这一点就很方便了。熟悉EPA的人会很多,因为大家都很熟悉以太网,因此熟悉这个平台软件开发的人就会很多,研发成本就会很低。这也是我们所期待的。也许这样对我们而言不会带来太多的商业利益,但是用户那边的成本降下来了,这样我们就拥有了一个新的平台可以跟外国厂家竞争了。 浙大中控每年花在研发上的经费是很大的,我们高度重视技术创新,包括在DCS的研发,也包括在MES应用软件方面的研发方面,我们希望能给广大用户提供能为企业节能降耗、提升企业竞争力的先进技术和整体解决方案。 笔者题记: 一直以“跻身世界自动化强者之林”为奋斗目标的浙大中控,在发展高科技、实现产业化的同时为“以信息化带动工业化,用高新技术改造传统产业”正在做出卓越的贡献。在浙大中控成立初期,国内自动化行业几乎被国外产品所垄断。近年来,浙大中控逐步实现了与国外大型控制系统高端产品同台竞争,并在各行业的投招标中屡屡胜出,改变了大型生产装置的自动化系统长期依赖于进口的局面。近两年,浙大中控的国际化进程已经初显成效。继2001年8月,SUPCON JX-300X控制系统成功进入越南市场,到2004年2月,JX-300X系统在朝鲜原油联合总会社30万吨常压蒸馏项目中成功中标……短短两年多来,带着“SUPCON”标志的产品在国际市场上初露锋芒。 EPA标准由浙大中控主持,联合浙江大学、中国科学院沈阳自动化研究所、重庆邮电学院、大连理工大学、清华大学、上海工业自动化仪表研究所等共同参与研发,并起草制定了《用于工业测量与控制系统的EPA系统结构与通信规范》,该标准业已经通过了TC124/SC4的技术审查。成为我国第一个拥有自主知识产权的现场总线国家标准并将提交IEC作为PAS标准予以发布。同时,该标准也被正在制定的实时以太网国际标准IEC61784-2收录。这是迄今为止,中国工业自动化领域第一个被国际认可和接收的标准。 浙大中控现已正式更名为中控科技集团有限公司。褚健先生任董事长兼总裁。 |
|
在线联系该厂商: |
关于“纵论DCS 展望EPA”,我有如下需求或意向: |
|
|